三菱电机2010年12月20日向新闻媒体公开了设置于该公司福山制作所内的配线断路器自动组装生产线。该生产线通过导入机器人使几乎所有的工序都实现了自动化,目前正在为2011年1月的**运转进行*终调试。三菱电机希望通过自动化来提高生产能力及生产效率,强化福山制作所作为面向海内外的供应基地的作用。
向海内外供货
福山制作所是三菱电机断路器的主力生产基地。三菱电机的断路器在日本国内份额高达约50%,其中的绝大部分均由福山制作所制造。由于生产量多,因此成本竞争力较高,还向海外出口。虽然三菱电机也在大连建有断路器工厂,但大连工厂的产品**于面向中国市场的小型产品等部分种类,而且远不及福山制作所的生产额。三菱电机表示,以福山制作所为主力的状态今后仍将继续保持下去。
不过,这一地位并非决对稳固。今后除了市场规模不断扩大的中国、印度及东南亚等地区对低价产品的需求将会增加之外,发达国家市场对价格的要求也将日趋严格,因此需要进一步提高生产效率。而能够在抓住这一增长需求的同时提高生产效率的手段就是组装工序的自动化。三菱电机2010年1月上市的新产品“WS-V”系列在此之前采用了以组装工序自动化为前提的设计,这也许意味着三菱电机将开始利用实际的自动化生产线来制造产品。
断路器主要由以下3个组件构成。
(1)开关机构组件
(2)可动元件组件
(3)交叉杆组件
(1)是用于手动实施开/关操作,或在过电流等流过时自动断开接触点(触点断开)的机构,在断路器中是*重要的功能组件。(2)是接受(1)的动作后可动的端子,有的断路器机型配有多个(具体数量与能够与断路器连接的布线数相同)。(3)是用于将(1)的动作传递给多个(2)这样���可动端子的机构。断路器的组装工序大体上就是对(1)~(3)实施的组装。
(1)~(3)组件的组装生产线的全景。照片由三菱
电机事先拍摄。公开当天不允许拍照。(以下相同)
(1)~(3)组件的组装生产线的细节部分
复杂构造成为障碍
原来福山制作所就已在(1)~(3)的组装工序上实现了自动化,但重要组件(1)的制造工序一直未能实现自动化。由于(1)即开关机构组件的工序此前委托外部企业来完成,因此占据了整个制造前导时间的绝大部分。具体而言,整个制造前导时间为5天,而开关机构的前导时间(从部件送至外部委托方到加工成组件后返回的时间)就占了4天。该制作所采取订购当天即向客户供货的机制,因此以往需要在工厂内确保产品库存。
用于制造开闭机构的机器人单元的全景
机器人单元的细节部分
开关机构组件无法实现自动化的原因在于组件构造非常复杂。组装实现自动化时,*理想的工序状态是能够按照相同的方向来连续层叠部件。不过,开闭机构组件有很多U字形部件,需要从不同方向来按照这些部件的构造,因此很难实现自动化。
为此,新产品WS-V系列采用了改变部分部件的形状等易于实现自动的设计。这样便可利用基于两台垂直6轴机器人的机器人单元来实施组装。具体操作时,先将开闭机构组件的部件(全部13个)装到托盘上,并将托盘输送至机器人单元,然后自动组装。虽然向托盘配置部件的作业以及托盘本身的输送作业以人工方式来完成,除此以外的工序全部实现了自动化。这样便将开闭机构给件的组装时间缩短到了依靠人工完成时的1/3,仅有30~40秒。今后的目标是利用机器人生产线而非机器人单元来制造。
实现更为缜密的管理
此外还通过基于二维码(QR码)的单品管理提高了整个组装生产线的灵活性,这也是生产线的一大特点。由于原来采用的是以批次为单位(1批约为20~1000个)的管理模式,因此在更换生产的产品种类时,需要在生产线上流过全部半成品,工艺转换时间需要6分钟之多。因此,从工艺转换的损失来考虑,1天可生产的产品种类以往以15种为界限。而此次通过实施单品管理,工艺转换时间几乎接近为零,因此新产生线可将1天的生产品种增至40种。另外,三菱电机还新开发了用以实现灵活制造的多工位方式的托盘交换装置。
除了上述单品管理之外,还通过在逐台制造设备上设置PLC(可编程逻辑控制器),实现了对品质及能耗等的极为缜密的掌握。在品质方面,能够通过管理计测值的偏差趋向来尽早发现异常及**产品,或者根据停机次数及停机原因的记录来迅速制定出改善对策。福山制作所也许是原来就在制造计测仪器等节能设备的缘故,以前被定位于环保示范工厂,今后将成为在此基础上融合了***FA技术的示范工厂“e&eco-F@ctory”。
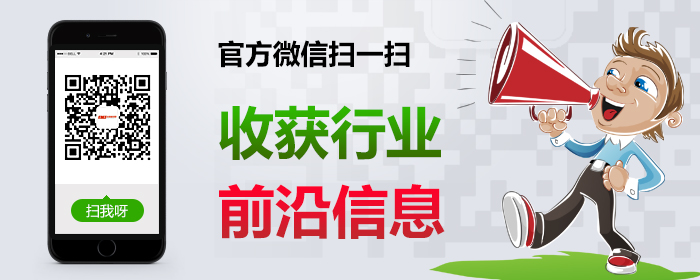