陶瓷材料,与金属材料和高分子材料并列为当今三大固体材料,具有高温强度突出、耐磨性能优越、隔热性好、密度低和防腐性能佳五大优势,在众多性能各异的工程材料中独树一帜[1]。但由于陶瓷材料具有硬度高、韧性差、可加工性差等缺点,高精度、复杂陶瓷构件加工难度大,成本高,因此复杂的陶瓷零件多采用胶态成形工艺制造[2],但是这类工艺均需要模具使陶瓷浆料成形,而复杂零件的模具制造周期长,成本高,影响成形精度的工艺因素多,无法满足单件小批生产和零件原型制造的需求。基于快速成形的陶瓷零件直接制造工艺无需模具,可缩短制造周期,降低制造成本,因此成为陶瓷材料成形研究的热点[3]。在众多快速成形工艺中,光固化工艺具有成形精度高的优势,本课题选择了光固化工艺来直接制造陶瓷件,即陶瓷光固化技术(Ceramic Stereolithography,CSL)。
陶瓷光固化技术是将陶瓷粉末加入可光固化的溶液中,通过高速搅拌使陶瓷粉末在溶液中分散均匀,制备高固相含量、低粘度的陶瓷浆料,然后使陶瓷浆料在光固化成型机上直接逐层固化,累加得到陶瓷零件素坯,*后通过干燥、脱脂和烧结等后处理工艺得到陶瓷零件[4-6]。
光固化快速成形工艺在制作树脂原型方面已经比较成熟,但利用该工艺直接制造复杂陶瓷件(包括复杂陶瓷铸型)的技术,国内仅有清华大学对树脂基PZT陶瓷浆料的光固化工艺开展了初步研究[7],但未见后续研究的公开报道。国外已经有许多机构开展了相关研究。目前主要的研究机构包括法国的国立高等工业陶瓷学校(ENSIC-INPL)、国立高等化工学院(ENSCI) 、法国科学与技术交流中心 (ESTER Technopole)[8-10];意大利的拉察大学(Uniersità di Lecce)[11];美国的密歇根大学安娜堡分校(University of Michigan, Ann Arbor)[12-14];普林斯顿大学(Princeton University)[15-16];加拿大的多伦多大学(University of Toronto)[17]和日本的大阪大学(Osaka University)等[18-19]。上述研究机构多采用树脂基陶瓷浆料来成形陶瓷件,高固相含量树脂基陶瓷浆料的粘度较高,且在后处理中产生大量废气污染环境,因此本课题提出采用水基陶瓷浆料来制造陶瓷零件。
快速成形工艺作为一种材料累加成形工艺,其基本成形单元的特性将直接影响快速原型零件的成形精度。针对光固化工艺来说,单条固化线是基本成形单元,陶瓷颗粒的存在导致入射激光发生散射,使陶瓷浆料的固化特性与传统光敏树脂不同。本课题从水基陶瓷浆料单条固化线和单层固化成层型的角度出发,研究光固化成型机工艺参数(如激光功率、激光扫描速度) 对单条固化线轮廓(单条固化线宽、固化厚度等)的影响以及单层固化过程中扫描间距和扫描速度对单层固化厚度的影响,为选择合适工艺参数,进而改善陶瓷件的成形精度提供参考。
试验材料与设备
试验中采用水基陶瓷浆料作为光敏材料,包括预混液(含硅溶胶、丙烯酰胺、N-N'****丙烯酰胺、丙三醇)、1173(2-羟基-甲基苯基丙烷-1-酮) (光引发剂)、聚丙烯酸钠(分散剂)和二氧化硅陶瓷微粉,粒径分别为1.8μm、5μm和8μm。浆料中陶瓷微粉的重量比为68%。成形设备为陕西恒通智能机器公司生产的SPS450B光固化成型机,检测设备有VHX-600光学显微镜、激光功率计和光斑分析仪等。
陶瓷颗粒的散射与传统光敏树脂固化过程不同,陶瓷浆料中存在大量悬浮的陶瓷颗粒,这些陶瓷颗粒成为入射光的散射中心,引发多次散射,导致陶瓷浆料表现出与光敏树脂不同的固化特性,图1为光敏树脂和水基陶瓷浆料单条固化线截面轮廓的对比。
由图1可知,相对于光敏树脂,水基陶瓷浆料的固化线宽增大而固化厚度减小,固化轮廓较为扁平,导致该现象的原因在于大量陶瓷颗粒的多次散射改变了激光束的传播途径,削弱了原传播方向上的曝光量,而增强了扫描线两侧的曝光量,从宏观上就表现为单条固化线的固化宽度增加。
陶瓷浆料的单条固化线
单条固化线是*基本的成形单元,因此本课题把水基陶瓷浆料的单条固化线作为研究对象。由于陶瓷浆料的单条固化线较为纤细,在清洗过程中易变形,影响试验结果测量的准确性。为此,本课题提出了一种避免单条固化线变形的方法,即利用零件支撑来制作单条固化线,从而提高其整体刚度,具体过程及试验结果如图2所示。
由图2可知,获取水基陶瓷浆料单条固化线可采用以下步骤:先利用CAD软件设计一个带凹陷的正方体;在数据处理软件中手动添加正交支撑;然后在成型机上成形包含支撑和周围增强结构的一层;*后将固化后的单层取出小心清洗干净,干燥后将即可获得单条固化线。将单条固化线截取,然后将断面放在光学显微镜下观察截面形貌,并测量固化线宽和固化厚度。该方法优点是:成形速度快,单片整体强度较高,处理方便,可避免单条固化线的变形。
(1)不同扫描速度ν对单条固化线宽Lw、固化厚度Cd及截面轮廓的影响。
由于激光在陶瓷浆料表面的曝光量随扫描速度变化(若激光功率不变),因此扫描速度的变化会影响单条固化线的固化轮廓。使用上述方法获得不同扫描速度ν下单条固化线的试样,利用光学显微镜观察截面轮廓,表1为不同扫描速度时单条固化线宽度Lw与厚度Cd的一组测量值。
由表1的测量结果可知,当激光功率固定时,单条固化线线宽Lw、固化厚度Cd均随扫描速度ν的增大而减小,与光敏树脂类似。但散射作用使得入射激光的固化厚度变小,固化宽度增大,且固化宽度均大于固化厚度,表明在入射激光与水基陶瓷浆料的散射和吸收作用中,散射现象占据主导地位。随扫描速度ν增大,Cd/Lw比值增大,说明随着扫描速度增加,激光在陶瓷浆料中的能量密度降低,导致陶瓷浆料的散射作用减小。
根据试验数据,可得单条固化线线宽Lw和固化厚度Cd与扫描速度ν之间的关系,如图3所示。
由图3可知,随着扫描速度的增加,入射激光在陶瓷浆料液面的曝光量随之降低,导致固化线宽和固化厚度随扫描速度增加而降低,尤其当扫描速度低于2000mm/s时。通过在Origin中进行曲线拟合,可发现单条扫描线的固化宽度、固化厚度与扫描速度之间为负指数关系。
(2)陶瓷浆料光敏参数Dp和Ec的确定。
衡量光敏材料的光敏特性参数一般有2个:一是陶瓷浆料的临界曝光量,即使陶瓷浆料转变为凝胶态的*低曝光量(Ec);二是陶瓷浆料的透射深度(Dp),即入射激光在传播方向上的曝光量降为液面1/e处离液面的距离。这两个参数反映了该光敏材料对于激光的吸收能力及固化难易程度,因此测定特定陶瓷浆料的Ec和Dp就显得非常重要。
其中,Dp为透射深度,是陶瓷浆料固相含量、粒径及陶瓷颗粒与预混液折射率之差的函数;E为激光在陶瓷浆料表面的曝光量;Ec为陶瓷浆料的临界曝光量,与光引发剂、单体系统及陶瓷固相含量有关,可以通过测量陶瓷浆料的固化厚度及曝光量,利用公式(1)得到这2个参数。曝光量E的表达式为
其中,P为激光在陶瓷浆料表面的功率(由功率计测得为270mW),w0为激光在陶瓷浆料表面的半径(由光斑分析仪测得为70μm),ν为激光扫描速率,可在光固化成型机中直接设定。在光固化成形机上改变扫描速度,使其从1500mm/s增至4000mm/s,测量单条线固化厚度,根据公式(2),得出曝光能量E、扫描速度ν及固化厚度Cd的关系如表2所示。
根据表2中数据,以曝光量E和固化厚度Cd值分别为横坐标和纵坐标,在Origin软件中进行数值拟合,可得到二者的拟合直线如图4所示。
由此,可得该陶瓷浆料的光敏参数:透射深度Dp=60.95μm,临界曝光量Ec=e2.76=15.8mJ/cm2。与常用光敏树脂(如DSM的Somos14120)相比,其临界曝光量Ec为6.8 mJ/cm2,穿透深度Dp=0.12mm,可知高固相含量水基陶瓷浆料的穿透深度小于光敏树脂,而临界曝光量大于光敏树脂。
将公式(2)带入公式(3)中,可得:
公式(5)中扫描速度ν的单位为mm/s,Cd的单位为μm,该公式即为当激光功率P为270mW时,单条固化线厚度Cd与扫描速度ν间的计算公式。为验证该公式是否正确,将试验数据与公式(5)的预测结果进行对比,图5给出了该公式预测结果和实际测量结果的对比。
由图5可知,当扫描速度位于1000~4000mm/s的范围内,公式(5)的预测结果与试验测量结果基本吻合,因此可以使用该预测模型预测不同扫描速率下的单条线固化厚度,为选择扫描速度提供依据。
单层固化特征
为确保光固化成形工艺的持续进行,就必须保证相邻层的粘接,即单层固化厚度必须大于分层厚度,因此工艺参数对水基陶瓷浆料单层固化厚度的影响规律研究就非常必要。为防止水基陶瓷浆料固化单层在清洗过程中出现变形,采用与上述制作单条固化线相同的方法制作单层固化层,减小扫描线的间距就可得到单固化层,随后将其洗净干燥后,在光学显微镜下观察单固化层的截面轮廓。
通过光学显微镜观察,可获得不同线间距下单固化层的截面轮廓图像。根据该方法制作不同扫描间距和扫描速度条件下的水基陶瓷浆料的单固化层并测量固化厚度。根据测量结果,得到单层固化厚度与扫描间距及扫描速度的关系,如图6所示。由图6可知,当扫描间距Hs>0.2mm时,Ld与Cd差距较小,当Hs≤0.2mm时, Ld就远大于Cd,这表明扫描间距对于单固化层固化厚度的影响较大,在选择工艺参数时,应优先考虑。当Hs>0.2mm时,只有当扫描速度低于1000mm/s,Ld才有可能大于200μm。成形过程中的相邻层粘接要求单层固化厚度Ld必须大于200μm,若选择较大的扫描间距,可能不利于提高成形效率。
工程应用
作为结构陶瓷和功能陶瓷,陶瓷材料在多个领域都有巨大的应用潜力,但是成形的困难导致其应用受到严重制约。陶瓷光固化工艺能够实现结构可控的复杂陶瓷件的快速直接制造,且其制造成本与陶瓷件的复杂程度无关,因此能够大幅降低复杂陶瓷件的制造成本,促进陶瓷材料在更多领域得到应用。
(1) 陶瓷零件。
相对于传统的金属零件,陶瓷零件的耐磨性、耐腐蚀和高温性能等异常突出,适合用于特殊的工况条件下,如高温热交换器、陶瓷叶片、叶轮等。利用陶瓷光固化工艺可制造结构复杂的陶瓷零件,与传统陶瓷制造方法相比,其周期短,成本低,力学性能近似。图7为西安交通大学利用陶瓷光固化工艺制作的陶瓷叶轮和叶片的素坯。
(2)精密铸造。
熔模铸造工艺可实现航空发动机叶片等的精密铸造,但是铸型的制造工艺复杂,影响叶片铸型质量和精度的因素较多,导致叶片的成品率较低。陶瓷光固化工艺使叶片铸型的型芯、型壳的一体化制造成为可能,无需熔模铸造制壳过程中的挂浆、撒沙、脱蜡、型芯和型壳装配等繁琐步骤,不仅极大地简化了铸型的制造过程,而且能够成型具有更复杂外部型面和内部结构的叶片铸型。该项研究在航空发动机空心涡轮叶片的精密铸造方面具有广阔的应用前景,西安交通大学先进制造技术研究所对此已进行了前期的研究,图8为利用水基二氧化硅陶瓷浆料制造的叶片铸型。
(3) 组织工程。
形态仿生制造与结构仿生制造是组织工程与人工关节实现功能仿生的重要方法。人体骨骼具有外部形态不规则,内部微结构复杂的特点。以往的制造方法与工艺难以满足其特殊强度及结构形态要求。生物陶瓷浆料的直接光固化工艺具有可控性强、加工精度高、成品率高等特点,避免了采用凝胶注模工艺成形过程中出现的浆料分布不均、干燥,脱模等流程中出现的断裂等问题,简化了生物陶瓷制品制造的工艺流程,缩短了制造时间,提高了具有微结构及不规则外部形态的生物陶瓷制件的制造精度与生物性能。
(4) 光子晶体。
光子晶体是介电常数不同的两种材料在空间按照一定的周期排列所形成的一种人造“晶体”结构,其基本特性包括光子禁带、光子局域和特殊的光学特性,*早是由美国的E.Yablonovitch和S.John在1987年分别在研究如何抑制自发辐射和无序电介质材料中的光子局域时各自独立提出的[20]。光子晶体*初是在光学领域提出的,但是由于光学波段的尺度很小,加工工艺要求高,所以人工制作光子晶体存在一定的困难。后来这种周期性通过缩放关系扩展到微波领域,加工上的难题不复存在[21]。光子晶体在微波、天线和光学等多个方面都有应用,如用于制作滤波器、波导、谐振腔、天线等。图9为西安交通大学利用陶瓷光固化工艺制造的金刚石结构三维光子晶体,日本大阪大学对该工艺在光子晶体制造方面也开展了系统研究[18-19]。
结 论
本课题提出了一种快速获取水基陶瓷浆料单条固化线和单固化层的方法,并研究了水基二氧化硅陶瓷浆料的光固化特性,通过研究得到以下结论:
(1) 散射是影响水基陶瓷浆料固化特性的重要因素,使得水基陶瓷浆料表现出与光敏树脂不同的固化特性。
(2) 单条扫描线的固化线宽和固化厚度均与扫描速度之间呈现负指数关系,与光敏树脂的规律类似,但是其固化线宽远大于其固化厚度,表明陶瓷浆料与激光的相互作用中散射占据主导地位。
(3) 水基陶瓷浆料的临界曝光量Ec大于普通光敏树脂,而穿透深度Dp小于光敏树脂,因此固化水基陶瓷浆料需要更高的曝光量。
(4) 扫描线间距和扫描速度之间的搭配关系影响陶瓷浆料的单层固化厚度,当水基陶瓷浆料的扫描线间距小于0.2mm时,若扫描速度小于2000mm/s,其单层固化厚度大于200μm;当扫描线间距大于0.2mm时,扫描速度低于1000mm/s时才能使单层固化厚度大于200μm,表明工艺参数选择可能影响到陶瓷件的成形效率,因此在工艺参数选择过程中必须权衡两者之间的关系。
(5) 陶瓷浆料直接光固化成形是解决复杂结构陶瓷零件制造的有效途径,该技术在复杂陶瓷叶片、陶瓷铸型、光子晶体、生物骨支架等方面都有良好的应用。这一技术将成为快速成形制造新的发展方向。
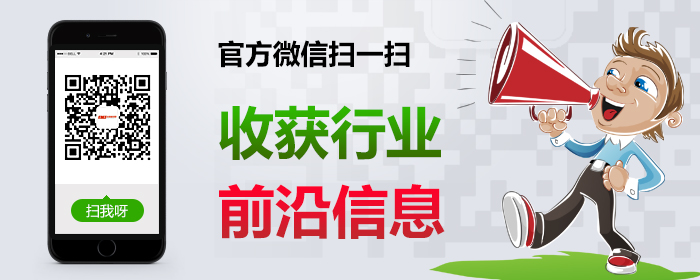