——未来极富潜质的成形和加工技术
由于制造过程的不断**以及整合、使用高强度材料等级,有紧密联系的车辆**和成形技术可以在更大程度上被实现。另外除去有限元仿真和优化工具的和谐使用,未来冲撞性能和可成形轻结构连同*佳材料的使用都可以得到提高。这意味着不仅可以直接影响车辆的**性能,制造成本也同样可以被降低。
由于制造过程的不断**以及整合、使用高强度材料等级,有紧密联系的车辆**和成形技术可以在更大程度上被实现。
车辆的**性和冲压技术互相协作
将车身制造技术发挥到**要求车辆的**性和冲压技术互相协作。来自于汽车测试和当今车辆的外观变形要求希望设计师和制造工程师(特别是冲压工程师)为未来道路的使用者们研制低成本、高**的汽车车身。
对新研发的可能解决方案的反复测试使得快速和有目标执行的系列化生产成为可能。在这里,我们来了解一下碰撞的相关部件、冲压制造方法例如冷和热冲压,还有零部件性能和制造系统优化的解决方案的要求。
结构和**性
轻结构和**性正如在各种车身制造中表现得那样,是现代汽车工业中两个主要议题。 利用汽车测试来对乘客车辆的**性进行持续评估,已经促使了新的制造替代方法和高强度材料的结合,而这是白车身一个重要的组成部分。
使用在变形技术(碰撞测试或者碰撞测试中产生的变形)中产生的方法,冲压技术的根本改革能够被实现。持之以恒的推行使用性能(碰撞)和制造工艺之间的交叉结合是由Frank-Stronach-Insitute成立并实现的。车辆**协会(The VehicleSafety Institute)与工具和冲压协会(Tools And Forming Institute)之间已经建立起各学科之间的广泛合作,目的是优化碰撞过程中的性能和轻结构以及探索如何降低生产成本。
为了这个目的,现代实验和测试仪器已经出现并且促进了不同供应商之间的合作(例如钢铁生产商、机床生产商、冲压和加工、FE软件的程序编写或者软件优化等)以及在这个领域内需要不断改进的专业技术。
来自碰撞的要求
在车辆**性中*重要的目的就是在碰撞情况下为乘客提供**完善的保护,因此更多的要求就需要由车辆结构来实现。复杂的高品质和高强度金属板材冲压零部件已经被应用于防止车辆框架的倒塌。不同的测试规则告知汽车制造商哪个部件需要抵挡住静态或者动态的力来避免乘客的危险。例如,A气囊在FMVSS216或者车顶冲撞性能实验中是被暴露在极大的应力下的。在该测试中,一个相当于整个车重1.5倍的力静态施加在A气囊的上方。车顶的变形度不应超过127mm(见图2)。假如这个测试在敞篷车上进行,一种没有车顶主支撑架作为附加支撑部件的车,使用复杂的变形部件(采用高强度等级的钢铁板材进行实验)是不可避免的。不过,达到必需硬度时的极限归结于特定的几何形式,因为一方面A气囊如果太宽就会减小驾驶员领域的视野;另一方面,设计的参数也只允许一块很小的搭建区域。
另外一个例子,施加在B气囊上的力是由一个重达950kg的滑车以相对于车辆50km/h的速度运动来实现的。一个由6个独立连接的铝质蜂窝状结构件构成的挡板被安装在滑车的前端,挡板的下沿离地面有300mm(如图3)。冲撞的能量一定被车辆的侧方结构所吸收,并且向内变形度应该保持在*小从而保护乘客的**。B气囊的坚固性是这次实验的基本内容。B气囊被暴露在折弯力、拉伸力和扭力下。另外,**带的再定向单元被放置在B气囊上,(当发生碰撞时)气囊上必须有一个6kN的力施加在一个特定的点上。实现能够承受这个动态应变材料的焊接并且实现复杂几何形状的加工,代表着板材冲压技术面临的严峻挑战。
冷金属板材冲压和热金属板材冲压
如今,已经有了两种被证实的并适用于“*高强度”系列生产中的金属板材冲压方法,他们是:高强度材料冷冲压和硼合金加压淬火。
冷冲压分为两种形式:单个部件的加工和序列合成工具的加工。方法的选择取决于拉伸的深度和使用的材料等级。
热冲压同样也分为两种方式:直接和间接冲压淬火。同时,该物理过程(例如从奥氏体到马氏体的转化)是两种方法的共同目的。
两种方法之间*大的不同在于使用的半成品。在直接冲压淬火时,简易成形毛坯被加热到奥氏体的温度,*终的几何形状在拉伸用具下成形,然后(成形之后)结构转化至马氏体的导向冷却开始。
对于直接冲压淬火来说,热镀铝钢(还有未涂层材料)可以被使用。使用热镀铝钢的好处是在材料的加热和转移过程中避免金属熔渣的形成。这个举措可以帮助阻止金属熔渣在冲模上的沉积,它能够负面影响工具的磨损。另外,炉内也不需要使用惰性气体。
间接冲压淬火时,在热成形过程中,冷成形部件被当作半成品使用,目的是减少在冲压过程中冲模和毛坯之间由于强相对运动而导致的冲模表面的磨损。
决定一个部件是采用冷冲压还是热冲压取决于车辆的造价或者重量的优先级别。如果价格的因素优先,那就使用冷冲压。然而,随着零部件复杂程度的提升,只有初始应力减少的材料才能被使用,这样就导致了使用金属板材厚度的增加(见图4)。如果优先考虑重量的因素和应力的高要求,那么热冲压的方法首当其冲。
工具技术
在毛坯的分离和定中心之后,他们被放在一个连续退火炉的传送带上。在这个炉内,毛坯跨越了不同的加热区域并且被加热到奥氏体温度。
系列炉深度的选择取决于被加工部件的光谱。通常,计划使用通用可行的设备是不明智的,因为退火炉的使用规划是根据*大的质量流量确定的,所以对于小零件来说(低质量流量)不划算,因为加热处理设备需要更高的投资和花费。另外的加热方法,例如耦合线圈加热会更具优势。
奥氏体的板材一旦离开加热设备的送出皮带就必须马上放置在冲压工具里,因为薄板材的热量损失速度可以达到20 30 °K/s。在马氏体初始温度一达到就要马上进行冲压,否则会出现裂缝(由马氏体生成时的高强度和低易成形性导致)。
冲压过后,零件被冷却到由奥氏体到马氏体的转变温度。该冷却过程占用了大量的周期时间,因此也具有减少成本的*大潜力。
冲压淬火设备的**概念
硼合金板材的冲压淬火连续生产为**提供了许多可能,他们都能同现今发展的**设施和成形概念紧密联系起来。
降低投资的花费和冲压淬火的周期时间对于零部件成本有着直接的影响。周期上每一秒钟的节省都能够导致零部件单价5%的削减。如今,普通的周期,包括加工,需要10 15s。
令人感兴趣的解决方案已经阐述完毕,它的结构图如图7所示。钢线圈在退火炉中加热并且原材料也被加热到奥氏体温度。随后综合加工、分离和冲压淬火依次进行。单件的锁定发生在边带的剥离之后。这种理念的*大优点是设计简单、低投入成本和空间的*小需求。
不过,必须对这些概念的实现进行可行性研究。
未来的工作进展
抛开改进现有工具概念的研究,工具和冲压协会现在正致力于对新型工具概念的研究(例如层状金属板的冷加工)。
对直接和间接冲压淬火技术的改进由有限元方法保证。
除了提高对冷却沟槽的布置和避免过度疲劳,对于热成形工具的计算目的还在于保证毛坯在工具中不同的冷却速度,因为零件的性能会被结构的调整而影响(纯马氏体结构或者混合结构)。使用热成像照相机的测量证实了这些结果并且展示出目前仿真工具继续发展的可能。
耦合过程计算和工具性能研究的目的是为了硼合金钢等级热成形的热力学计算。它考虑了在材料冷却和零件使用特点决定微结构发展的情况。
除了这些方法,现在还出现了一种新的概念,用DMD方法的顺序耦合来执行冷却金属的铣削。另外,还有把该方法与热传导金属的软芯交叉使用的可能(例如表面带一层防磨损层的铜)。
车辆**性的仿真质量
为了预测车辆受冲撞时的性能,大家在仿真质量上投入了大量的人力物力。零部件的生产过程在其中发挥了重要的作用,因为*终零部件的性能将直接影响于此。在冲压过程中,板材被拉薄,塑应力在材料上累计并加强,*终的加工件还有一定的残留应力。烘烤强化过程发生在喷涂过程中并且材料的拉力也有增加,因此,将这些结果从生产过程中准确地转移到冲撞仿真中就能大大地提高仿真结果的质量。
将结果从成形仿真转移到冲撞仿真的过程是由所有主流冲撞仿真软件都可以提供的映射运算法则来实现的。正常的步骤是将厚度和有效塑性力的网点从细小成形网格映射至大冲撞网格。根据材料和部件的几何结构,在冲撞模式下,这将导致更软或更硬部件的反应。更硬的反应通常发生在冷冲压部分。在热冲压部分,因为奥氏体/马氏体的转化,累积的塑性力不会导致任何硬化发生。
展望
由于制造过程的不断**以及整合、使用高强度材料等级,有紧密联系的车辆**和成形技术可以在更大程度上被实现。另外,除去有限元仿真和优化工具的和谐使用,未来冲撞性能和可成形轻结构连同*佳材料的使用同样可以得到提高。这意味着不仅可以直接影响车辆的**性能,涉及到制造成本的机构也同样能够得到很大改进。
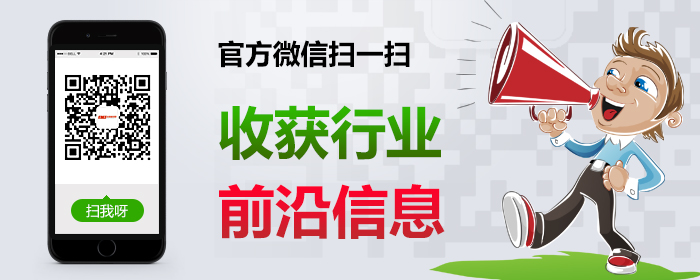