神龙公司和国内许多其他公司焊装车身线成形工位一样,采用了多种成形机技术,通过对这些工艺方式的运用和特点进行对比和总结,可为今后的车身成形定位机工艺设计提供参考意见。
焊装车身线是焊装车间车型生产的主要生产线,对于它的设计,需要慎重考虑以下几点:
1.平面位置的重要性。它是车型各部分总成的集成线,对零件的物流、生产组织和运行以及厂房设计起着决定性的作用。
2.产品演变的适应性。为适应市场对汽车产品需求由以往的单一性向多样性的转变,对车身线的柔性化生产也提出了更高的要求,其设计方案需结合产品规划而考虑。
3.投资利用率。由于车身线一次性投资较大,设计时需尽量考虑其设备的再利用率和产品演变后的改造费用。
车身线的核心就是成形定位工位,采用不同形式的成形定位技术对该线的生产品种、生产节拍、占位面积、平面布置、投资以及今后的产品升级都起着决定因素,由此可见对成形工位的设计和分析就显得十分重要和必要。
目前神龙公司焊装车间主要采用的成形机技术有:Flex framer成形机(ABB)、Body flexor成形机(CFER)以及Geoflexor成形机(PCI)。在二工厂X7项目规划时,我们还考虑了国内其它的两种成形机技术:Opengate成形机(COMAU)和Geotack成形机(ETAG)。本文将对这几种成形机技术做简单的介绍和分析。
Flex framer成形机
Flex framer成形机的主要特点是通过机器人搬运成形工装,然后用工装组合对车身进行定位。定位过程中,左、右侧部工装和后部工装之间相连接,成为一个整体框架。机器人通过抓取不同的工装进行合装来实现对不同车型的成形,从而实现多种车型在同一工位的柔性化生产。目前这种成形机在我公司202车间使用,共线生产T11/T21/T33和将来的T31车型。
1.工艺参数
整个成形��工位由3个工位组成,生产线长20m,宽15m。其中主工位长8m,宽15m。 Flexframer节拍时间目前可达到21V/H,*大的产能可达到34V/H,*大产能通过减少本工位焊点或增加焊接机器人实现,前提条件是保证必要的成形焊点。
受现有工位面积的限制,Flex frame工位能容纳3套不同的左部、右部以及后部工装(见图1),下部工装能适应两种不同的底盘。组合后可达到成形6种不同车型的能力。
2.结构组成
整个成形机系统由机器人、定位工装、滚床、车身自动升降装置以及可梭动下部工装5部分组成。其中机器人分别承担抓取定位工装和焊钳进行车身定位和焊接的功能。Flex framer采用4套定位工装进行成形,分别为左部、右部、后部以及下部。其中左部、右部、后部工装为机器人抓取工装,可梭动下部工装通过前后工位的移动,可实现两种不同底部工装的转换。详细的结构组成如图2所示。
3.主要工作步骤
导入并固定雪撬—滚床降到中间位—翻板A合上—滚床降到低位—带工装机器人(R2R5R6)运动到**个等待位—底部工装B组压头夹上—机器人(R2R5R6)继续前进,停留在**个等待位—工装互锁—底部工装其他压头夹上—机器人工装压头前进到位—工装机器人脱开并取焊钳,其他机器人焊接—成形点焊接完成—机器人与工装联接并激活摸块—机器人工装压头打开—互琐松开—机器人取走工装,回到初始位—其他4台机器人完成后续焊点的焊接。
4.几何精度的保证
工装的定位精度并不取决于机器人的重复到位精度(±0.5mm),而是依靠底部工装的楔型槽与互锁头的定位面为机器人工装的定位基准。在侧部和后部工装设有测量基准点,通过底部坐标系的建立对这些工装上测量球的测量,从而确保定位工装的装配精度。
5.定位互锁机构
FLexframe 互锁机构是ABB公司的**产品,在成形定位机上共有7个,其中底部工装定位连接4个,上部工装定位连接3个,其重复定位精度为±0.1mm。
Body flexor成形机
Body flexor成形机同Flex framer类似,也是通过机器人搬运组合工装,实现对车身的定位。其不同之处在于其侧部工装和底部工装的结构形式,其左、右侧部工装分为前后两个独立部分,这对于同一车型的两箱、三箱车转变更具灵活性。其底部工装不具备FLexframe 成形机前后梭动功能,不同车型的底部变化通过底部工装支撑定位机构的三维可移动机构来实现,目前我公司的X7和BX3项目的车身线成形机采用此项技术。
1.工艺参数
整个成形机工位(见图3)生产线长10m,宽13m。*大节拍理论通过增加机器人和减少成形焊点数量达到55V/H(14台机器人),前提条件是保证必要的成形焊点,此*大节拍尚未在现有车型上得到验证。
目前在X7项目中,节拍设计能力为28V/H,有98个成形焊点,共使用8台机器人(MOTOMAN),如采用ABB机器人需再增加2台,这主要是由于受机器人臂长和载荷限制的原因。在BX3项目中,节拍设计能力为33V/H,有85个成形焊点,共使用10台机器人(ABB),通过增加1 台机器人可使该工位的生产能力达到38V/H。在阿根廷的B51/B53 项目上,节拍设计能力为30V/H,共有70个成形焊点,使用5台机器人(FANUC),如采用ABB机器人则需要7台。
Body flexor 成形工位能容纳3套不同的前后侧部工装,下部工装通过底部支撑定位机构的三维可移动机构理论上能适应多种不同的底盘,组合的结果可达到6种以上车型的能力。
2.结构组成
整个成形机系统由机器人、侧部定位工装、下部定位工装、滚床和车身自动升降装置组成(见图4)。其中左、右侧部工装分前后两部分,底部工装的支撑定位机构可设计成三维可移动机构。
3.定位互锁机构
Body flexor工装的定位精度同样不取决于机器人的重复到位精度,而是依靠底部工装与侧部工装的连接互锁系统的定位面做为机器人工装的定位基准,其定位原理与Flex framer类似。
Body flexor互锁机构系统ZPS(ZERO POINT SYSTEMS)是CFER与德国AMF公司共同研制的**产品,其定位是依靠销轴通过四周镶嵌环绕的球体传递尺寸来限制其X/Y/Z方向,重复定位精度为±0.1mm。在成形定位机上共有12个,其中底部与侧部工装定位有8个连接互锁,侧部前后工装上部定位各有2个连接互锁。
Geo flexor成形机
Geo flexor成形机是PCI公司传统的成形机产品,该成形定位技术在PSA汽车集团被广泛使用,具有结构刚性好、几何定位稳定、不同车型转换快以及生产效率高等特点。目前我公司的T63/T61/B53/B51四种车型均采用此成形机技术,并已实现同一工位共线生产。
1.工艺参数
Geo flexor成形机由三个工位组成,工艺面积为生产线长18.5m,宽11m,其中主工位长6.5m。由于该工位的机器人仅进行焊接,没有搬运零件的时间消耗,因此生产能力很大,可以通过减少成形焊点的数量达到*大50~55V/H 的生产能力。
目前我公司T63/T61/B53/B51生产线经过三次改造,成形工位节拍能力已达38V/H,共有100个成形焊点(理论上T/B的成形焊点*少仅为60个左右),使用8台焊接机器人。
Geo flexor采用上下两套工装进行成形,上部工装能适应4种车型变化,下部工装能适应2种不同底盘车型变化,组合的结果理论上可达到成形8种不同车型的能力。
2.结构组成
整个成形机系统由固定龙门、上部工装、可梭动的下部工装、四面体工装转换系统以及滚床升降装置构成。上部工装通过固定龙门的空中旋转体实现四种不同车型的快速转换,下部定位工装分左右两个独立部分,采用坦克链驱动移动装置实现两种不同底盘车型的前后移动转换。
3.主要工作步骤
导入并固定雪撬—底部工装按车型运动到位—上部工装旋转体按车型旋转到位—滚床降到低位—上部工装脱离旋转体落在龙门定位—EXPERT系统脱离—工装定位加紧—机器人开始焊接—焊接结束,定位工装夹头打开—EXPERT系统锁定上部工装上升—升降滚床升起,雪橇向前行走。
4.对几何精度的保证
(1)基准坐标系的建立。用成形机立柱上的8个基准球建立坐标系,通过安装在成形机传输方向中心线上的激光测量跟踪仪来实现,精度达到0.01mm。
(2)上部工装的基准面测量。利用激光测量跟踪仪对上部工装的基准面进行测量,共有9个测量点。
(3)下部工装的基准面测量。利用激光测量跟踪仪分别在左右下部工装传输中心线上对下部工装的基准面进行测量,左右各有6个测量点。
需要指出的是,Geoflexor成形机的旋转移动定位依靠3套EXPERT机构,有效地保证了**分度定位,重复性精度很高,从而使成形机的整体重复性精度达到±0.1mm。
Opengate和Geotack成形机
Opengate成形机技术是意大利COMAU公司在1993年推出的产品,主要是靠左右侧部工装对车身进行定位,机器人不参与定位,仅进行焊接。通过左右侧部工装的更换,实现多种车型在同一工位的生产是该成形机柔性生产的原则,至今该技术已经过了5代技术演变。
由于Opengate 成形机侧部工装更换较快(行走机构速度2m/s),机器人仅进行焊接,生产能力强,*大可达48~55V/H 的生产能力。
整套定位机构由左、右侧部工装、底部定位工装、滚床及车身自动升降装置构成。具体机构组成如图5所示。工装的刚性较好,不易产生变形,稳固可靠,定位较为**。
Opengate成形机的侧部工装通过堆栈行移形式,可实现多种车型的侧部工装更换(见图6),但多品种时占地面积较大,需要合理考虑布局。
Opengate成形机技术在FIAT、GM、FORD等汽车公司的焊装生产线成形工位被大量采用,在我公司X7项目前期方案咨询过程中,该成形机技术也做为候选方案参加投标。
Geotack成形机技术是德国ETAG公司的产品,其车型变换的工作模式与Opengate比较类似,也是依靠侧部工装的转换来实现同一工位的柔性生产。该成形机与Opengate的不同之处在与其侧部工装采用独立的翻转式工装合装机构,工装的结构设计十分牢靠稳定,使车身定位的几何尺寸得到有效的保证。
Geotack成形机*多可在同一工位实现6种车型的柔性生产,其侧部工装的转换排布上更具有智能化,整个工位在传输线长度方向为18m,宽度为14.5m,占地面积比Opengate小。由于此成形机技术具有生产节拍大、车型柔性化好、几何尺寸稳定以及后期车型导入对现生产影响较小的特点,因此在大众等大型汽车公司被广泛采用。
几种成形机技术的对比
以上几种成形机都是比较成熟的技术,在生产的实践过程中都得到了验证,但针对不同的使用和需求情况,又具有各自的适应性。本人根据了解和现生产的使用情况做一个简单的对比(详见下表)。
随着汽车工业的发展,市场对车型品种的需求越来越多样化,单一品种在市场的占有率比重也在逐步减少,这就使以往的单一、高节拍汽车生产模式向品种多样、市场适应力较强方向演变,这使Flex framer和Body flexor比Geo flexor更具有一定的优势,至于Opengate和Geotack技术,由于受占地面积的影响,因此具有一定的局限性,这些也是神龙公司在后期的X7 和BX3 两个新项目中选择Bodyflexor 成形机技术的主要原因。
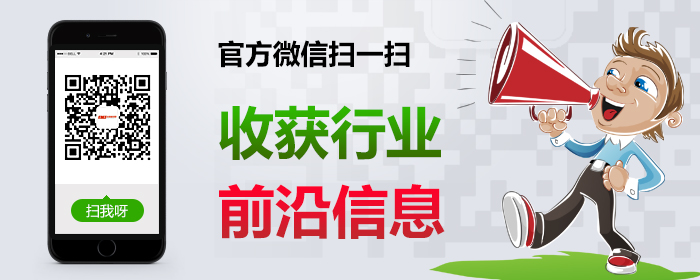